(585)775-5289

Portable Wind Tunnel
Built for my senior design project
NIAC 2020
Scholarship Winner
NASA Innovative Advanced Concepts merit scholarship winner 2020
I earned a scholarship, generously awarded by NIAC, a section of NASA dedicated to investigating potential missions and technologies.

Rapid Mask Finalist
​
The Navy office of Tech Solutions 2020 search for a mask design
My lab was contacted to rapidly produce a 3D printable mask design for the navy. That task was delegated to me, and I created 5 mask designs that could be 3D printed and would hold a filter material specified by the Navy. My design was considered until the end of the selection process where the Navy chose their own in-house design.
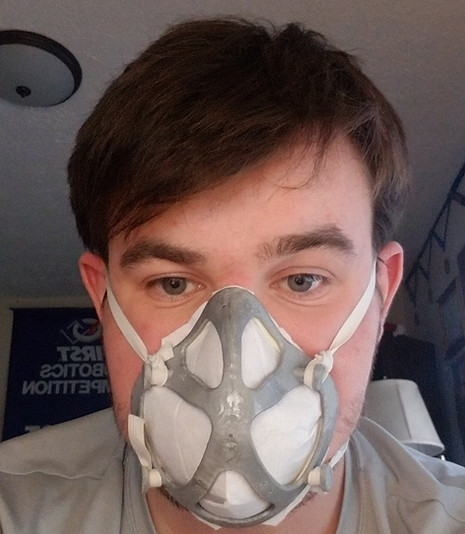
That is me :)
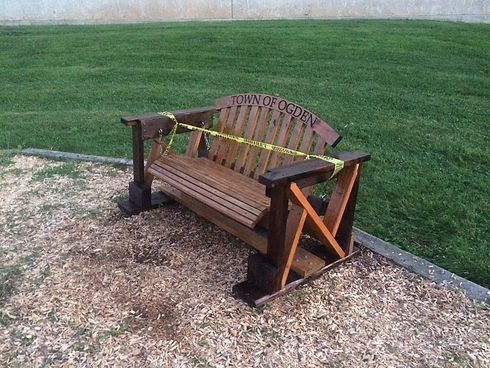
An Old Classic
My 2017 Eagle Scout project
On this site, I have an archive of most of my major projects (the ones that worked anyway).
​
I have a page detailing the design and construction of my Eagle Scout project. This project was a milestone for me in that I earned a rank I had long sought, but also, I had the privilege of leading a team through the construction of something I designed myself.
Class Projects
​
A look at what I have learned
I have a selection on this website of class projects that I am allowed to publish (I cannot share many class examples due to academic integrity concerns).
Please browse the skills that I have developed while taking classes. The university projects folder on the top of the screen will bring you to specific examples, or you can start with this video (to the right) and use the link below.

ABOUT ME
Hi! My name is Matt Thornton, I just graduated with a Mechanical Engineering degree from the State University of New York at Buffalo. I'm looking for a career that will utilize my engineering and CAD skills.
​
The tabs above will guide you through the projects I have worked on for the past 10 years. A quick highlight gallery featuring some of my favorite projects is available below.
SKILLS


CAD
I love CADing, I have experience with a variety of programs but am most familiar with Autodesk Inventor. All of the projects on this site were CAD'd by me and accurately reflect how my skills have grown in recent years.

3D MOUSE
I have been using these for a while now and they have been integrated into my workflow. I have a Space Navigator with side buttons (2015) and a Space Mouse (circa 2005). I am a pro with spatial navigation and can go with or without the buttons.


3D PRINTING
I have made thousands of parts using about 15 miles of plastic filament. When I started the machines would break down between prints and every setting was critical to creating a usable product. While printers are easier to use now the experience of using them when it was hard has made me a better engineer as I can MacGyver my way out of a problem.
TOOLS
I am very practical, and I have mastered a wide assortment of tools. Hammers and pliers are a given, I am referring to tap sets or angle grinders.
​
Part of the challenge of making new designs is learning how to use complicated equipment, but that opens up a world of new possibilities. For example, I learned how to use a lathe a few years back and that introduced me to lots of radially symmetrical possibilities.

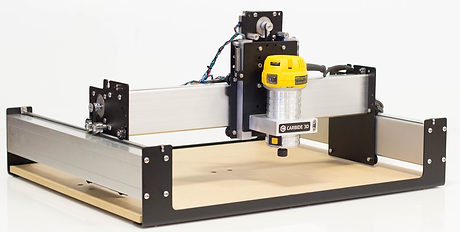
CNC
My gcode experience isn't limited to printing. I know how to use a few CAM programs and I am happy to learn more.
​
I have carved out of aluminum, wood, nylon, polycarb, and construction foam.
​
The most complicated cut that I have made was a 3D Captain America shield. The part was made out of a square block of material that had a rough followed by a fine waterline excavation on the top and bottom. Challenges faced were getting both excavations lined up and concentric. This was done by having a defined zero location through preplanned mounting of the block,
​
Another challenge was keeping the thin end product from breaking while in production. Breakages were mitigated by the use of high spindle rotation and a relatively low feed rate.
Hololens
Proudly self-taught in using this device, I had the single goal of being able to view colorized 3D holograms in real space. I tinkered for a few weeks until I found a viable series of exports, programs, and edits that rendered multicolored assemblies from this AR headset.
​
This device has been useful in seeing how objects would look in different environments. I have placed holograms around me to gauge how well they are scaled and planned to exist before I spent any money on materials and the time cost of construction.
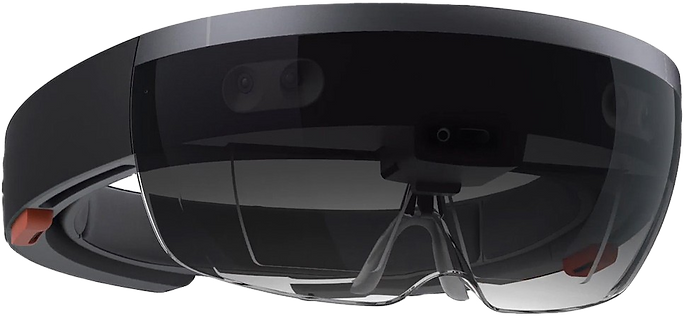
Milling
While working at Carrier I found that my projects would get done much faster if I was willing to machine them myself. I was taught how to manufacture using engineering drawings while operating a mill.
